Mastering Combustion Simulations with ANSYS CFX: A Comprehensive Guide
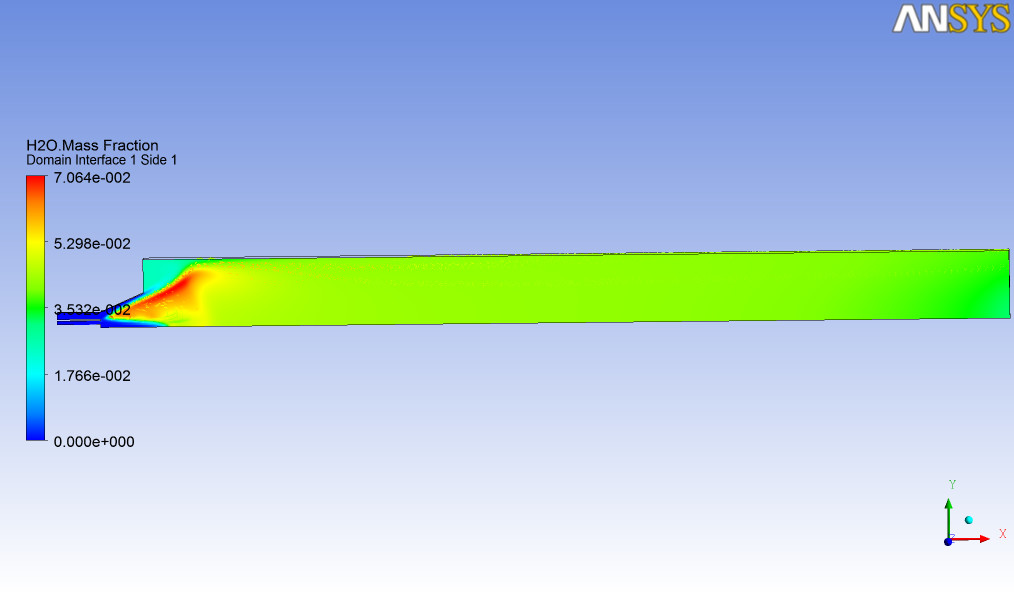
Introduction: Combustion processes play a vital role in various engineering applications, including energy generation, propulsion systems, and industrial processes. Simulating combustion phenomena accurately is essential for optimizing system performance, minimizing emissions, and ensuring safety. ANSYS CFX is a powerful computational fluid dynamics (CFD) software package widely used for simulating complex flow and heat transfer phenomena, including combustion processes. In this comprehensive guide, we will explore the intricacies of simulating combustion processes in ANSYS CFX, covering everything from fundamental combustion principles and modeling techniques to practical simulation setups and advanced analysis strategies.
Section 1: Introduction to Combustion Processes 1.1 Understanding Combustion: Combustion is a chemical reaction between a fuel and an oxidizer, typically oxygen, resulting in the release of heat, light, and products such as carbon dioxide, water vapor, and other combustion byproducts. Combustion processes can occur in various configurations, including premixed, diffusion, and partially premixed combustion, depending on the mixing characteristics of fuel and oxidizer.
1.2 Importance of Combustion Simulation: Simulation of combustion processes is crucial for understanding flow behavior, heat transfer, and chemical reactions in combustion systems. Computational fluid dynamics (CFD) tools such as ANSYS CFX enable engineers and researchers to model and analyze complex combustion phenomena, optimize combustion chamber designs, and predict performance and emissions characteristics of combustion devices.
Section 2: Fundamentals of Combustion Modeling 2.1 Combustion Chemistry: Combustion involves complex chemical reactions between fuel and oxidizer species, leading to the formation of combustion products and release of heat energy. In ANSYS CFX, combustion chemistry is typically modeled using reaction mechanisms and kinetics models to simulate species transport, reaction rates, and combustion kinetics accurately.
2.2 Turbulent Combustion Modeling: Turbulence plays a significant role in combustion processes by enhancing mixing, heat transfer, and reaction rates. ANSYS CFX offers turbulence models such as the Reynolds-averaged Navier-Stokes (RANS) equations, large eddy simulation (LES), and detached eddy simulation (DES) for modeling turbulent combustion flows and capturing turbulence-chemistry interactions.
Section 3: Modeling Approaches for Combustion Simulation 3.1 Eddy Dissipation Model (EDM): The Eddy Dissipation Model (EDM) is a widely used combustion model in ANSYS CFX for simulating turbulent combustion processes. EDM assumes that the reaction rate is proportional to the turbulence kinetic energy dissipation rate, allowing for efficient simulation of combustion without explicitly resolving all chemical species and reactions.
3.2 Finite Rate Chemistry (FRC): The Finite Rate Chemistry (FRC) model in ANSYS CFX solves detailed chemical reaction mechanisms to simulate combustion chemistry accurately. FRC considers the transport of individual species, reaction kinetics, and heat release rates, making it suitable for modeling complex combustion processes with detailed chemical kinetics.
Section 4: Combustion Simulation Setup in ANSYS CFX 4.1 Geometry Preparation: Before setting up a combustion simulation in ANSYS CFX, users need to prepare the geometry of the combustion chamber or device using CAD software or ANSYS DesignModeler. The geometry should include all relevant components, such as fuel injectors, combustion zones, and heat transfer surfaces.
4.2 Boundary Conditions: Boundary conditions define the inlet, outlet, and wall conditions of the combustion simulation domain in ANSYS CFX. Users specify boundary conditions such as mass flow rates, temperatures, pressures, and species concentrations at inlet and outlet boundaries, as well as wall boundary conditions for heat transfer and wall reactions.
Section 5: Combustion Simulation Settings and Solver Setup 5.1 Solver Settings: In ANSYS CFX, users configure solver settings such as numerical discretization schemes, convergence criteria, and solution methods for solving the governing equations of fluid flow, heat transfer, and combustion. Proper selection of solver settings is essential for obtaining accurate and reliable simulation results.
5.2 Initialization and Solution Monitoring: Users initialize the combustion simulation in ANSYS CFX by specifying initial conditions such as flow velocities, temperatures, and species concentrations. During the solution process, users monitor convergence, solution stability, and key performance metrics to ensure the simulation progresses smoothly and yields meaningful results.
Section 6: Post-Processing and Analysis of Combustion Simulations 6.1 Visualization of Results: After completing the combustion simulation in ANSYS CFX, users visualize and analyze simulation results using post-processing tools such as CFD-Post. CFD-Post provides visualization capabilities for displaying flow fields, temperature distributions, species concentrations, and combustion reaction rates in graphical formats.
6.2 Analysis of Performance and Emissions: Users analyze performance metrics such as combustion efficiency, heat release rates, temperature profiles, and species concentrations to evaluate the performance of combustion systems and assess emissions characteristics. ANSYS CFX allows users to quantify pollutant emissions such as NOx, CO, and unburned hydrocarbons to comply with environmental regulations.
Section 7: Advanced Analysis and Optimization Strategies 7.1 Sensitivity Analysis: Sensitivity analysis in ANSYS CFX involves varying input parameters such as fuel composition, operating conditions, and geometry configurations to assess their impact on combustion performance and emissions. Sensitivity analysis helps identify key factors influencing combustion behavior and optimize system design parameters accordingly.
7.2 Combustion Optimization: Combustion optimization aims to improve combustion efficiency, reduce emissions, and enhance system performance through design modifications and operational adjustments. ANSYS CFX supports optimization techniques such as design of experiments (DOE), response surface methodology (RSM), and genetic algorithms for optimizing combustion systems and achieving design objectives.
Section 8: Real-World Applications and Case Studies 8.1 Gas Turbine Combustors: In gas turbine engines, combustion simulation with ANSYS CFX is used to optimize combustor designs, enhance fuel-air mixing, and minimize emissions while maximizing combustion efficiency and stability. Engineers simulate turbulent combustion in gas turbine combustors to predict flame characteristics, combustion dynamics, and pollutant emissions.
8.2 Internal Combustion Engines: In automotive and transportation applications, ANSYS CFX is employed to simulate combustion processes in internal combustion engines (ICE) such as spark ignition (SI) and compression ignition (CI) engines. Simulation of combustion in ICEs helps engineers optimize fuel injection strategies, combustion chamber designs, and engine operating conditions to improve fuel efficiency and reduce emissions.
Section 9: Future Trends and Developments 9.1 High-Fidelity Combustion Modeling: As computational resources and simulation capabilities continue to advance, future developments in ANSYS CFX may focus on high-fidelity combustion modeling with increased spatial and temporal resolution. High-fidelity simulations enable detailed analysis of combustion phenomena, including flame propagation, ignition, and pollutant formation, leading to improved accuracy and predictive capability.
9.2 Multiphysics Coupling: Integration of combustion simulations with other physics phenomena such as heat transfer, acoustics, and solid mechanics is an emerging trend in computational combustion modeling. Multiphysics coupling in ANSYS CFX allows users to simulate complex interactions between combustion processes and other system components, leading to more comprehensive and accurate simulations of real-world applications.
Conclusion: ANSYS CFX is a versatile and powerful tool for simulating combustion processes in engineering applications, offering advanced modeling capabilities, accurate numerical algorithms, and comprehensive post-processing tools. By mastering the techniques and best practices outlined in this guide, users can leverage ANSYS CFX to simulate and analyze complex combustion phenomena, optimize system performance, and achieve design objectives in various industries. With its intuitive interface, robust solver capabilities, and active development, ANSYS CFX continues to be a preferred choice for engineers and researchers seeking to advance their understanding of combustion processes and improve combustion system designs.