How to Implement Quality Control
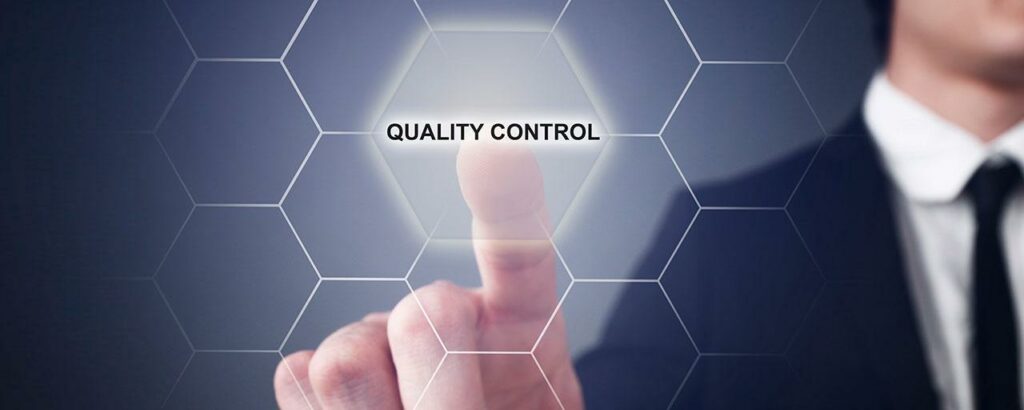
Implementing quality control is essential for ensuring consistency, reliability, and customer satisfaction in products or services. Quality control (QC) processes involve systematic measures to monitor, assess, and improve processes, outputs, and outcomes to meet defined standards and expectations. This comprehensive guide will outline essential steps, best practices, and strategies to help organizations implement effective quality control measures.
Importance of Quality Control
Quality control is crucial for several reasons:
- Customer Satisfaction: Ensures products or services meet or exceed customer expectations, leading to increased satisfaction, loyalty, and repeat business.
- Operational Efficiency: Identifies and addresses defects, errors, or inefficiencies early in production or service delivery, reducing waste, rework, and costs.
- Compliance: Ensures compliance with industry standards, regulatory requirements, and legal obligations, minimizing risks and liabilities.
- Brand Reputation: Upholds and enhances brand reputation by consistently delivering high-quality products or services that reflect reliability, trustworthiness, and value.
- Continuous Improvement: Facilitates continuous improvement initiatives by providing data-driven insights, identifying opportunities for innovation, and enhancing organizational effectiveness.
Key Steps to Implement Quality Control
1. Define Quality Standards and Objectives
- Set Quality Goals: Establish clear quality objectives, benchmarks, and performance metrics aligned with organizational goals, customer requirements, and industry standards.
- Specify Quality Criteria: Define measurable quality criteria, specifications, tolerances, and acceptance criteria for products, processes, or services to ensure consistency and compliance.
2. Develop a Quality Control Plan
- Plan Structure: Create a structured quality control plan outlining roles, responsibilities, procedures, and workflows for implementing quality control measures.
- Process Mapping: Map out key processes, workflows, and critical control points (CCPs) where quality checks, inspections, or tests will be conducted to monitor and verify quality.
3. Implement Quality Assurance Practices
- Quality Assurance (QA) Systems: Establish QA systems, methodologies, and best practices to prevent defects, ensure adherence to standards, and verify compliance with regulatory requirements.
- Documentation and Records: Maintain accurate records, documentation, and traceability of quality control activities, test results, inspections, audits, and corrective actions taken.
4. Conduct Quality Inspections and Testing
- Sampling Plans: Develop sampling plans (e.g., random sampling, stratified sampling, attribute sampling) to assess product quality, performance, and conformance to specifications.
- Testing Protocols: Define testing protocols, methods, and procedures for conducting physical, chemical, mechanical, or performance tests to validate product quality and safety.
5. Establish Quality Control Checks and Reviews
- In-Process Inspections: Perform in-process inspections at various stages of production or service delivery to identify defects, deviations, or non-conformities early in the process.
- Final Inspection: Conduct final inspections, audits, or reviews before product release or service delivery to ensure all quality requirements, standards, and customer expectations are met.
6. Implement Corrective and Preventive Actions (CAPA)
- Root Cause Analysis: Investigate and analyze root causes of quality issues, non-conformities, or customer complaints using tools such as fishbone diagrams, 5 Whys, or Pareto analysis.
- CAPA Plans: Develop and implement corrective actions to address immediate issues and preventive actions to mitigate future risks, improve processes, and prevent recurrence.
7. Monitor, Measure, and Improve
- Quality Metrics: Define and monitor key performance indicators (KPIs), metrics, and benchmarks to track quality performance, trends, and continuous improvement initiatives.
- Quality Audits: Conduct regular internal audits, external audits, or third-party assessments to evaluate adherence to quality standards, effectiveness of QC measures, and compliance with regulations.
Best Practices for Implementing Quality Control
- Leadership Commitment: Secure commitment and support from top management to prioritize quality as a core value, allocate resources, and promote a culture of quality excellence.
- Employee Training: Provide comprehensive training, skill development, and certification programs to empower employees with the knowledge, skills, and competencies needed to perform quality control tasks effectively.
- Continuous Learning: Foster a culture of continuous learning, innovation, and improvement by encouraging employee feedback, sharing best practices, and implementing lessons learned from quality initiatives.
- Customer Feedback: Solicit customer feedback, reviews, and satisfaction surveys to gain insights into customer perceptions, expectations, and opportunities for enhancing product or service quality.
- Supplier Partnerships: Collaborate closely with suppliers, vendors, and partners to establish quality agreements, specifications, and performance metrics, ensuring consistency and reliability of incoming materials or services.
Conclusion
Implementing effective quality control measures is essential for achieving consistency, reliability, and customer satisfaction in products or services. By defining quality standards, developing a structured QC plan, implementing QA practices, conducting inspections and testing, implementing CAPA processes, monitoring performance, and embracing best practices, organizations can enhance product quality, operational efficiency, and competitiveness in the marketplace. Investing in robust quality control initiatives not only strengthens organizational capabilities but also fosters trust, loyalty, and long-term success by delivering products or services that consistently meet or exceed customer expectations and regulatory requirements.